Numerical Simulation of Multi-Liquid Impinging Jets Using Volume of Fluid Method
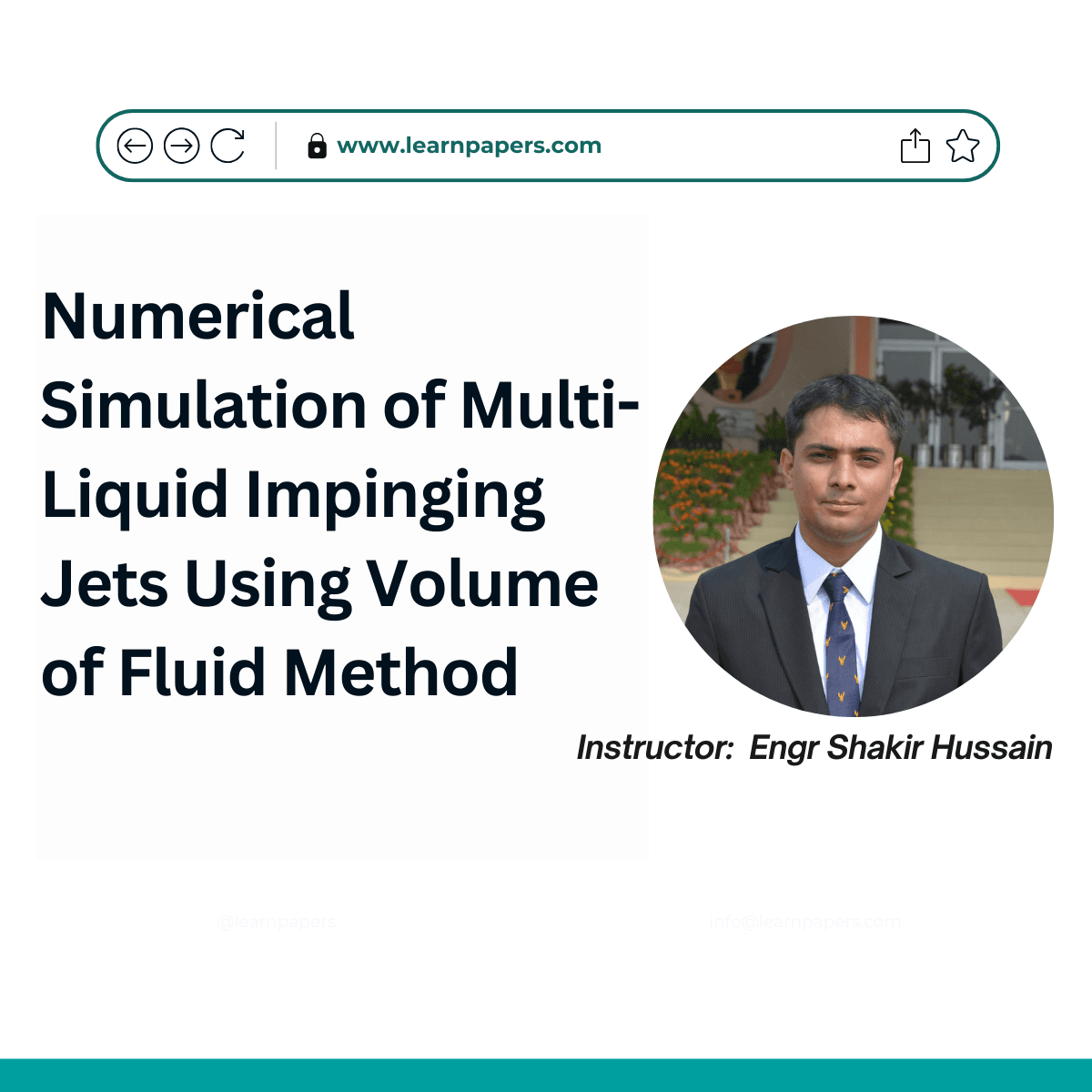
About Course
The “Numerical Simulation of Multi-Liquid Impinging Jets Using Volume of Fluid Method” course provides an in-depth exploration of multiphase flow modeling using Computational Fluid Dynamics (CFD). This course focuses on impinging jet atomization, a crucial process in fuel injection systems, combustion chambers, and industrial spray applications. Learners will gain a solid understanding of the Volume of Fluid (VOF) method, which is widely used to track liquid-gas interfaces in high-fidelity simulations. Through hands-on training with ANSYS Fluent, participants will learn how to set up CFD simulations, define boundary conditions, optimize mesh refinement, and analyze breakup patterns in multi-liquid jets.
This course is designed for CFD researchers, aerospace engineers, mechanical engineers, and graduate students looking to expand their expertise in multiphase flow simulations. It covers essential topics such as turbulence modeling, adaptive mesh refinement, numerical validation, and user-defined functions (UDFs) for advanced customization. By the end of the course, learners will be able to conduct accurate, high-resolution simulations of liquid impingement processes, compare numerical results with experimental data, and apply their knowledge to real-world engineering applications such as fuel injectors, spray systems, and rocket propulsion technologies.
Abstract:
Liquid propellant rocket engines are an important part of space program. To achieve optimum performance and stability in case of liquid propelled rocket engines, good atomization and mixing characteristics of the fuel and oxidant are required. Injector element design based on impinging jet phenomenon for mixing and atomization are the ideal choice for engines using storable liquid propellants. This is due to their simple fabrication, good spray and mixing characteristics. In this paper, CFD technique was applied to numerically investigate the flow characteristics of impingement process of two liquid jets using Volume of Fluid (VOF) method with appropriate surface tension modeling for capturing liquid/gas interfaces. Different meshing techniques such as structured meshing with Adaptive Mesh Refinement and Coarsening were employed to efficiently capture the flows areas containing liquid/gas interfaces. Simulations results were compared with experimental results which are available in literature and flow patterns formed by liquid sheet breakup are also studied by comparing it with the experimental results.
Link: